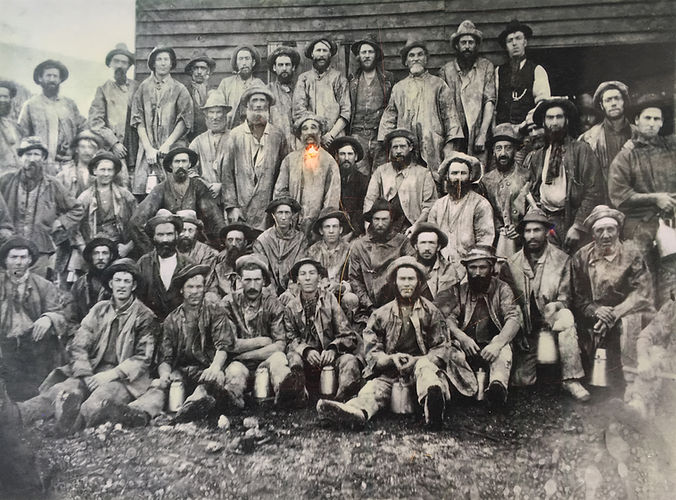
Industrial Strength
The Pumping Power at Berry No.1 Mine
Confronted with unprecedented volumes of water flowing into their mine, the Berry No. 1 Company had no choice but to erect some of the most extensive pumping operations in Victoria. The vertical Cornish Beam Pump that worked here played an important role in the development of Victoria’s manufacturing industry and was a major achievement for 19th century engineering.

PUMPING CAPABILITY
227,000L
PER HOUR
PUMP BEAM WEGHT
50 tonnes
50,000 KILOGRAMS
DEPTH OF SHAFT
+180m
600 FEET
Under the pump
​
Despite being a good proposal on paper, the location of the Berry No. 1 mine had the unfortunate reality of being in an exceptionally wet part of the Berry Lead.
​
As with many of the surrounding mines, work was often suspended for long periods except for operating the boilers, engine and pumps that tirelessly worked to drain the flooded mine and to keep the water at a workable level.
​
The pump with the necessary power to lift these significant volumes of water and the people with the technical knowledge to coordinate it were from Cornwall as it was in the wet Cornish tin and copper mines that the Vertical Beam Pump had been designed, developed and refined.
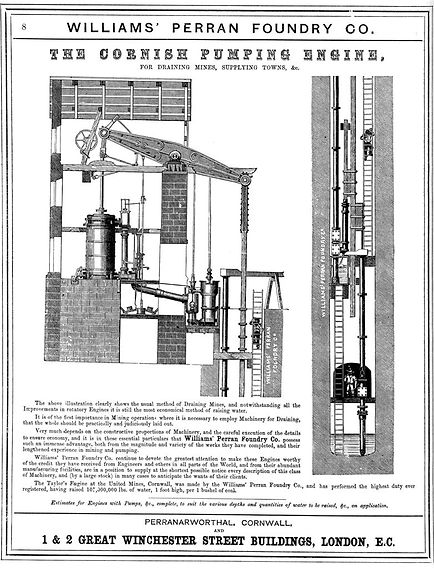

But even with this advanced technology the ‘forces of nature’ were always against the mine as bursts of heavy drift smashed the timbers in the drives and clogged the company’s pumps.
Local engineering
​
Although not an entirely original design, the engine and beam pump installed at Berry No. 1 were a crucial reminder that mining companies were prepared to engage local foundries to build these complex machines, rather than importing them from England.
​
The technological task was awarded to John Hickman’s Union Foundry in Ballarat, however the directors of the Berry company were also doubtful that the firm could fulfill the contract, so they required Hickman to enter into a £1000 bond that the engine would be completed to their satisfaction.
​
The Union Foundry delivered on their promise and in 1883 were contracted to build another engine for the Hepburn Estate mine.

Above: Cross section of the Berry No. 1 Pump Engine based on Annual Report of the Secretary of Mines, 1885 and Rex Bridge’s 1883 model of the pump house which is displayed at the Creswick Visitor Information Centre. Drawing by Robt Haughie.
“This firm had mastered the skills necessary for what in the 19th century was a piece of high technology. At this point Victorian engineering came of age.” Dr. P. Miller

Above: A shift on the steps of the pumphouse’s arched opening to the engine room. Photos: Creswick Museum

Above: Berry No. 1 Mine, showing the three storey brick and bluestone pumphouse.

Above: A plan section of Berry No.1’s ~6m x 4m shaft. Note the area or the winding shafts (1), used to raise and lower the cages, compared with what was required for the pump and cisterns (2). Source: Annual Report of the Secretary of Mines, 1885
The pumphouse remains
​
The photo opposite shows the scale of the beautiful brick and bluestone engine house.
At approximately 15 metres high and built on foundations three metres deep, it was estimated by a local bricklayer that close to a million bricks were used in its construction.
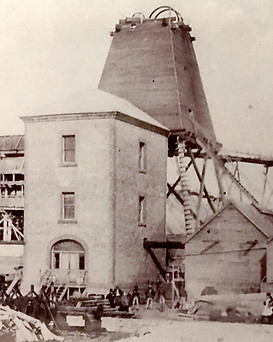

Photo: Terry Hope

Berry Gold Mining Co.
​
Berry No. 1 was the goldfield’s ninth largest gold producer and unfortunately for shareholders and owners it was a poor investment.
Registered in 1881, it took three years for the contractors to bottom the shaft and a further six years elapsed until the first gold was won.
​
When the company closed in 1898, 58% of the total operating costs went to wages and contracts, 12% on fuel for the boilers and only 1.3% was paid as dividends (£5,000 from calls of £140,000).

Above: Berry Gold Mining Company's flag.